Battery X Metals, together with its partner, a global top 20 university, achieves a milestone and achieves a graphite recovery of 98.6% and a metal oxide purity of 96.3%

Key facts of the press release:
- With its self-developed two-stage flotation process, Battery X Recycling Technologies achieves a graphite yield of 98.6% and a metal oxide purity of 96.3% – a decisive milestone.
- The combination of a new solvent and two-stage flotation enables more efficient separation and less interference with the binder, thus achieving considerable success in process optimization.
- In collaboration with the global top-20 university, the next phase of trials is being initiated, which will focus on further increasing graphite purity and oxide yield. The ultimate goal is patent protection and future commercialization for broad application in the lithium-ion battery recycling industry.
VANCOUVER, British Columbia - May 16, 2025 / IRW-Press Release / Battery X Metals Inc. (CSE: BATX) (OTCQB: BATXF) (FWB: 5YW, WKN: A40X9W) ("Battery X Metals" or the "Company"), a resource exploration and energy transition technology company, announces that its wholly-owned subsidiary, Battery X Recycling Technologies Inc. ("Battery X Recycling Technologies"), has achieved another graphite recovery and metal oxide ("MO") purity milestone in its ongoing research collaboration with the Institute of Mining Engineering at a global top 20 university (the "Global Top 20 University") for its proprietary environmentally friendly froth flotation technology under development.
Following the Company's press releases of April 4, 2025, and May 6, 2025, Battery X Recycling Technologies and the global top-20 university have gained important insights into their ongoing work to optimize the recovery of battery-grade raw materials from end-of-life lithium-ion batteries. This includes the identification of a new solvent (the "New Solvent") that enhances the selective removal of metal oxides from graphite using Battery X Recycling Technologies' proprietary environmentally friendly froth flotation process, the evaluation of different froth-to-collector ratios, and the implementation of both single-stage and two-stage flotation processes.
As previously announced in the press release dated May 6, 2025 (the "Previous Results"), the flotation tests on the black mass treated with the new solvent resulted in significantly faster separation in the flotation cell. This high degree of foaming suggests that some metal oxides were inadvertently carried into the graphite foam rather than remaining in the tailings as intended. To further investigate this effect and optimize separation precision, two follow-up runs were conducted using the concentrate (377 g) and tailings (105 g) from the previous results, which were obtained from flotation tests on 500 g samples of unoxidized, nickel-manganese-cobalt (NMC)-dominant black mass using Denver flotation cells (each a "Current Run" and collectively the "Current Runs").
These follow-up experiments consisted of the current Experiment 1, a reflotation of the graphite-rich concentrate, and the current Experiment 2, a reflotation of the corresponding tailings. Both experiments utilized a frother but no collector, and employed the same configuration of Denver flotation cells as in the previous results. In the current Experiment 1, flotation proceeded as rapidly but somewhat more controlled than in the previous experiments, with the graphite beginning to float even before aeration and foam forming within 2 to 3 minutes. In the current Experiment 2, on the lower-solids tailings—which consist largely of materials that do not naturally float—less severe foaming and a shorter duration of approximately 2 minutes was observed. The combined results of the current experiments were used to calculate the results (as defined here).
The tests showed a remarkable performance improvement compared to the previous results: The graphite recovery increased from 96.28% in the previous single-stage test to 98.6% in the two-stage flotation, corresponding to a relative increase of 2.4% and an absolute increase of 2.32 percentage points. The graphite content improved from 72.99% to 75.7%, corresponding to a relative increase of 3.7% (an absolute increase of 2.71 percentage points). The metal oxide yield (in the residues treated as metal oxide concentrate) increased from 48.09% to 53.2%, corresponding to a relative increase of 10.6% (an absolute increase of 5.11 percentage points). And the metal oxide content increased from 89.87% to 96.3%, corresponding to a relative increase of 7.1% (an absolute increase of 6.43 percentage points) (collectively, the "Results").
The results relate to the measured improvements in graphite yield, graphite content, metal oxide recovery, and metal oxide purity achieved by applying a two-stage flotation process designed to reduce carryover and improve selective separation. These improvements represent a significant advance in process performance compared to previous results and were determined using the same graphite burn-off method, in which samples were heated to 750°C for two hours to quantify the graphite content and calculate the associated material balances. A comparison between the previous and current results is presented in the table below.
Comparison of graphite recovery rate and quality
parameter | Current experiment: Non-oxidized sample - two-stage flotation, pre-wash with new solvent (foaming agent & collector) | Previous experiment: Non-oxidized sample - single-stage flotation, pre-wash with new solvent (foaming agent & collector) |
Graphite yield (%) | 98.60% | 96.28% |
Graphite content (%) | 75.70% | 72.99% |
Comparison of metal oxide recovery rate and quality
parameter | Current experiment: Non-oxidized sample - two-stage flotation, pre-wash with new solvent (foaming agent & collector) | Previous experiment: Non-oxidized sample - single-stage flotation, pre-wash with new solvent (foaming agent & collector) |
Metal oxide yield (%) | 53.20% | 48.09% |
Metal oxide content (%) | 96.30% | 89.87% |
Significance of the results and next steps in the ongoing research collaboration with the global top 20 university
The use of the new solvent in conjunction with the two-stage flotation process marks a significant advance for Battery X Recycling Technologies and its proprietary battery materials separation platform. By reprocessing both the concentrate and residue from the previous single-stage test, the company demonstrated significantly improved separation efficiency, achieving a graphite recovery of 98.6% and a metal oxide purity of 96.3%. These results reflect a significant improvement in flotation efficiency and selectivity and confirm that incorporating targeted chemical treatment with staged mechanical processing can effectively overcome previous limitations.
This development also builds on previous findings that a gummy binder in the black mass—believed to be a byproduct of real-world battery use—can hinder the proper separation of graphite and metal oxides during flotation. The new solvent promises to prevent this binder effect, while the two-stage flotation configuration has improved mechanical selectivity and contributed to more optimal separation of the materials. Overall, these innovations have led to improved recovery rates and higher product purity.
Battery X Recycling Technologies and the global top-20 university will focus the next phase of research on reducing the impact of this binder to further improve battery material recovery performance. The goal is to achieve even better graphite purity and metal oxide yield through improved pretreatment, more sophisticated solvent strategies, and continuous process optimization. In addition to minimizing the impact of the binder, future work will also focus on reducing mechanical entrainment and improving separation selectivity to maximize recovery efficiency. Battery X Recycling Technologies and the global top-20 university also plan to source and test black mass with different chemistries—including phosphate-dominant material—to evaluate the versatility and efficiency of the company's froth flotation technology for different battery compositions and recycling scenarios. The collaboration aims to validate the technology and file a provisional patent application to protect the underlying intellectual property, ultimately enabling the process to be commercialized for broad application in the lithium-ion battery recycling industry.
"These results represent a further advance in the development of our clean technology platform," said Massimo Bellini Bressi, CEO of Battery X Metals. "By combining a chemical and mechanical approach to separating battery materials, we are developing an environmentally friendly solution for end-of-life lithium-ion batteries. We continue to achieve significant milestones in our collaboration with this top-20 global university, and we hope this momentum continues."
Tailwind for lithium-ion battery recycling industry and importance of graphite extraction
Battery X Metals, through its wholly-owned subsidiary Battery X Recycling Technologies, is advancing sustainable lithium-ion battery recycling technologies through its amended research collaboration agreement with the global top-20 university. The research will focus on its proprietary froth flotation technology under development to recover critical battery materials such as graphite, lithium, nickel, cobalt, manganese, and copper from end-of-life lithium-ion batteries, thereby supporting a circular battery economy.
Graphite, which makes up 95% of lithium-ion battery anodes1, is often neglected in conventional hydrometallurgical and pyrometallurgical recycling methods2. Battery X Metals' process is promising, especially since it enables the deposition of cathode-active metal oxides from anode-active graphite without decomposition—in contrast to high-temperature treatments3 and chemical leaching processes4 such as pyrometallurgy and hydrometallurgy.
In October 2024, Mercedes-Benz (FWB: MBG) opened Europe's first battery recycling plant integrating mechanical-hydrometallurgical processes and became the first automobile manufacturer in the world to install its own battery recycling loop5, underlining the industry's shift towards battery recycling.
Further evidence of the industry's dynamism is that Redwood Materials Inc., founded by Tesla co-founder and former Chief Technology Officer JB Straubel, has been the exclusive battery recycling partner for Lime's shared scooters and e-bikes since April 2025. This collaboration, which spans operations in the US, Germany, and the Netherlands, aims to recycle used batteries, thereby improving the domestic supply of critical materials and optimizing battery recycling supply chains.6
Redwood Materials has also partnered with major companies such as Ford, Panasonic, BMW, General Motors, and Toyota. The company has received a $2 billion conditional loan from the U.S. Department of Energy to build and expand a battery materials campus in Nevada to support the growing electric vehicle market in America.7, 8
The global shift towards electrification is driving the transition to clean energy, with lithium-ion batteries playing a central role in reducing dependence on fossil fuels.9 Global demand for lithium-ion batteries is expected to increase by 670% by 203010, with the need for energy storage increasing from 700 GWh in 2022 to 4.7 TWh10 – primarily due to the increasing adoption of electric vehicles.10 Yet recycling remains underutilized, with less than 5% of batteries currently recycled.11 Electric vehicles and battery storage will account for almost half of the growth in mineral demand from clean energy technologies over the next two decades12, making the extraction of materials such as graphite, lithium, nickel, and cobalt fundamental.
As the industry prioritizes battery recycling, Battery X Metals' environmentally friendly technology captures battery-grade graphite anode material, which is often lost through conventional methods. This positions Battery X Metals to fill a critical gap in the growing battery recycling market.
1 ECGA, 2 National Library of Medicine, 3 Rho Motion, 4 LA Ist, 5 Mercedes-Benz ,6 TechCrunch , 7 Redwood Materials, 8 Ford Authority 9 Energy X, 10 Mckinsey & Company, 11 CAS, 12 Mining Review Africa
About Battery X Metals Inc.
Battery X Metals (CSE:BATX) (OTCQB:BATXF) (FWB:5YW, WKN:A40X9W) is an exploration and technology company focused on commodities for the energy transition. To this end, Battery X Metals is committed to advancing the exploration of domestic and critical battery metal deposits while developing proprietary next-generation technologies. With a diversified, 360-degree approach to the battery metals industry, the company focuses on the research, life extension, and recycling of lithium-ion batteries and battery materials. For more information, please visit batteryxmetals.com.
On behalf of the Board of Directors
Massimo Bellini Bressi, director
For further information please contact:
Massimo Bellini Bressi
Chief Executive Officer
Email: [email protected]
Phone: (604) 741-0444
Disclaimer for forward-looking information
This press release contains forward-looking statements within the meaning of applicable securities laws. These statements relate to the Company's objectives, strategies, and future plans, including the development, optimization, validation, and commercialization of proprietary technologies, exploration initiatives, and strategic collaborations. Specific forward-looking statements include, but are not limited to: expectations regarding the Company's ongoing research collaboration with a global top 20 university and future research plans under the collaboration; the performance, optimization, and potential benefits of the Company's proprietary froth flotation process; the expected impact of the new solvent on improving the selective separation of graphite and metal oxides; the role of multi-stage flotation in improving yield and purity; the significance of binder interference and efforts to mitigate its impact; the evaluation and testing of phosphate-dominated and other black mass chemistries; the scalability, applicability, and commercial viability of the Company's process for use in various battery compositions; and the intention to file a provisional patent to protect the intellectual property arising from the process. Other forward-looking statements include expectations regarding graphite recovery and quality, metal oxide purity and recovery, improvements in flotation efficiency and selectivity, and the Company's broader role in addressing critical mineral supply challenges through sustainable lithium-ion battery recycling. These statements also reflect management's belief that the Company's technology provides an environmentally friendly alternative to traditional pyrometallurgical and hydrometallurgical recycling processes and that the Company is well positioned to meet increasing global demand for battery-grade materials such as graphite, lithium, nickel, cobalt, manganese, and copper. Forward-looking statements also include references to general industry trends, such as the projected increase in global demand for lithium-ion batteries, regulatory developments supporting circular economy initiatives, and the role of leading automotive and battery recycling partnerships in shaping future market opportunities. These forward-looking statements are based on current expectations, assumptions, and beliefs as of the date of this press release. However, they involve known and unknown risks, uncertainties, and other factors that may cause actual results, performance, or achievements to differ materially from those expressed or implied herein. These risks include, among others: uncertainties in research and development; results of laboratory tests and trial programs; technical challenges in developing and scaling the Company's flotation process; regulatory and permitting risks; fluctuations in commodity prices; supply chain constraints; the ability to secure sufficient financing or strategic partnerships to advance commercialization; competition in the battery recycling and critical minerals sectors; dependence on external collaborators and suppliers; and changes in consumer preferences, industry standards, or geopolitical conditions affecting the adoption of clean energy technologies. Battery X Metals undertakes no obligation to update or revise any forward-looking statements to reflect future events, developments, or circumstances, except as required by law. Investors are cautioned not to place undue reliance on these forward-looking statements and are encouraged to refer to the Company's public disclosures on SEDAR+ for additional risk factors.
The original language (usually English) in which the original text is published is the official, authorized, and legally binding version. This translation is provided for ease of understanding. The German version may be shortened or summarized. No responsibility or liability is assumed for the content, correctness, adequacy, or accuracy of this translation. From the translator's perspective, this release does not constitute a recommendation to buy or sell! Please refer to the original English release at www.sedarplus.ca, www.sec.gov, www.asx.com.au/, or on the company's website.
The original English press release can be found at the following link: https://www.irw-press.at/press_html.aspx?messageID=79651 The translated press release can be found at the following link: https://www.irw-press.at/press_html.aspx?messageID=79651&tr=1NEWSLETTER REGISTRATION:
Current press releases from this company directly to your inbox: http://www.irw-press.com/alert_subscription.php?lang=de&isin=CA07135M2031 Message transmitted by IRW-Press.com. The sender is responsible for the content. Free reprinting permitted with attribution. https://www.wallstreet-online.de/nachricht/19363253-battery-x-metals-erreicht-gemeinsam-partner-globalen-top-20-universitaet-meilenstein-erzielt-graphitgewinnung-98-6-metalloxid-reinheitsgrad-96-3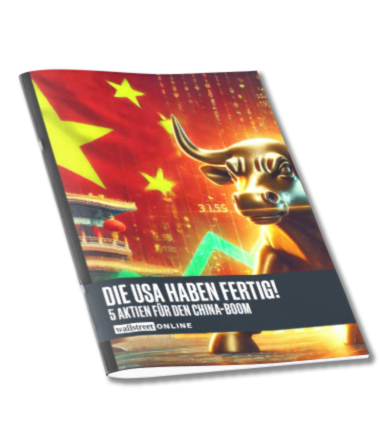
This exclusive offer is only valid for a limited time! So download it now!
nachrichten-aktien-europa